Recommended Procedures for Batching and Mixing FORCE 10,000D® Concrete – TB-0703
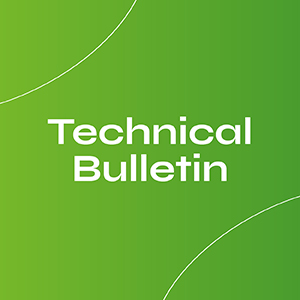
The key to producing high quality, high performance concrete with FORCE 10,000D® is thorough mixing. It is essential that FORCE 10,000D® is uniformly distributed throughout the concrete mixture and the densified silica fume broken up. This technical bulletin offers recommendations for batching and mixing FORCE 10,000D® concrete. The basic recommendations provided by ACI 304, “Guide for Measuring, Mixing, Transporting and Placing Concrete” should be followed for producing concrete; however, FORCE 10,000D® requires further batching and mixing details that will be discussed in this technical bulletin. The “Silica Fume User’s Manual” by the Silica Fume Association and printed by the Federal Highway Administration, FHWA-IF-05-016, contains good information for batching and mixing silica fume concrete.
Product Types
FORCE 10,000D® is available as a dry-densified powder, both in bulk and bagged. The bulk material is delivered into a silo at the concrete producer and added to the mix similar to cement. The bagged material is added, by hand, unopened t o the mixer since the bags are designed to disintegrate during mixing, or opened and then poured into the mixer.
Batching and Mixing
Bulk Material
FORCE 10,000D® as bulk silica fume should be weighed just like cement. However, care should be taken to avoid weighing errors due to the smaller amount of FORCE 10,000D® as compared to the larger quantities of other mix ingredients. Add the FORCE 10,000D® with the other cementitious material and other concrete ingredients. Never add the FORCE 10,000D® first into an empty drum or mixer with only water in the drum. Do not yet add the superplasticizer. Turn the mixer for 100 revolutions at mixing (charging) speed at a concrete slump of 50 to 100 mm (2 in. to 4 in.). This lower slump will eliminate the potential for silica fume or cement balls from forming and allow for uniform dispersion. After this mixing has taken place, add the superplasticizer to bring the mix up to the desired slump by mixing an additional 70 revolutions at mixing speed.
Bagged Material
FORCE 10,000D® is also sold in 11.3 kg (25 lbs) repulpable bags. These bags are designed to disintegrate in a mixer due to grinding and wetting of the paper during the mixing process. Note the condition of the bags before using. If the bags are wet, do not use them. Wet silica fume will not disperse correctly. Start by counting and setting aside the number of bags necessary for each truck. As an example, if the specification calls for a 5% replacement on a 385 kg/m3 (650 lbs/yd3) mix, then 13 bags of FORCE 10,000D® will be required for a 8 m3 (10 yd3) truck.
Inch/Pound Calculation
650 lbs/yd3 X 0.05 = 32.5 lbs/yd3 X 10 yd3 per truck = 325 lbs of FORCE 10,000D®. 325 lbs / 25 lbs/bag of FORCE 10,000D® = 13 bags.
Metric calculation
385 kg/m3 X 0.05 = 19.3 kg/m3 X 8 m3 per truck = 154 kg of FORCE 10,000D®. 154 kg / 11.3 kg/bag of FORCE 10,000D® = 13.6 bags. Use 14 bags.
Add the cement, aggregates and water to the mixer, but not the superplasticizer. Add the bagged FORCE 10,000D® to the drum. Never add the FORCE 10,000D® first into an empty drum or mixer with only water in the drum. Mix for 100 revolutions at mixing speed. Add the superplasticizer to bring the concrete up to the required slump and mix for another 70 revolutions.
There are instances when the bags may not completely disintegrate. This can occur in low water/cementitious mixes, mixes with coarse aggregate of 13 mm (½ in.) or less, rounded aggregate, or in pan mixers. If the concrete producer is concerned that this may occur, run a test with the proposed mix and view the results. If the bags do not disintegrate, then during concrete production open the bags and empty them into the mixer when the drum is not moving. Discard the bags.